Your trusted partner for warehouse safety
Use our interactive Cantilever Configurator to build your racking system in real time – and get a quick quote.
Why Racking Inspections Matter
Racking inspections are crucial for maintaining a safe warehouse environment. Regular inspections can reduce racking-related accidents by up to 30%, ensuring compliance with health and safety regulations like HSE’s HSG76.
Why Choose S.E.M.CO For Your Racking Inspections
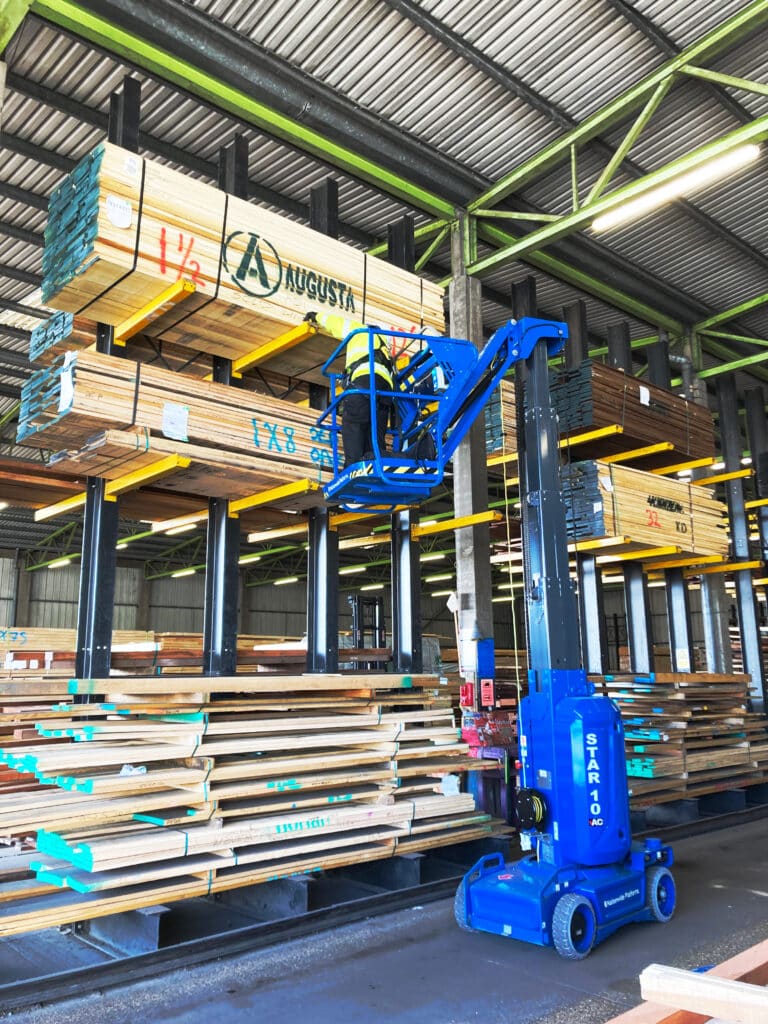
In-house SEMA Approved Racking Inspectors (SARIs) with specialised training: Our inspectors undergo rigorous SEMA training, ensuring they meet the highest industry standards for identifying and addressing racking issues, from minor wear to critical structural failures.
Full SEMA membership for industry-leading standards: As full SEMA members, we adhere to strict guidelines, giving you confidence that our inspections align with the latest safety and quality protocols recognised across the UK.
Comprehensive aftercare services to support your needs: Beyond inspections, we offer tailored maintenance plans, repair recommendations, and ongoing consultations to keep your warehouse compliant and operational.
S.E.M.CO are full members of SEMA (Storage Equipment Manufacturers Association), with our installation and inspection teams fully SARI (SEMA Approved Rack Inspector), and SEIRS (Storage Equipment Installers Registration Scheme) registered.
Our Inspection Process
We follow a thorough process to ensure your racking is safe:
Initial assessment of the warehouse layout: Our inspectors evaluate your racking configuration, including pallet types, load patterns, and aisle widths, to ensure compliance with manufacturer specifications and HSE guidelines.
Structural integrity and load capacity checks: We meticulously examine beams, uprights, and connectors to confirm they can safely support their designated loads, using advanced tools like laser levels for precision.
Identification of wear, damage, or misuse: From surface rust to overloaded racks, we document all issues, providing detailed notes on their severity and potential risks to your operations.
What Happens After the Inspection
You will receive:
A detailed report with our findings: A comprehensive document outlining all identified issues, categorised by the SEMA traffic light system, with clear photos and descriptions for transparency.
Recommendations for repairs or maintenance: Specific guidance on addressing issues, including prioritised actions for Amber and Red risks, and referrals to trusted repair services if needed.
Ongoing support to ensure compliance: Follow-up consultations and a conversation regarding training for your staff to maintain racking safety and prevent future issues.
Understanding the SEMA Traffic Light System
Green (Low Risk): Indicates minor issues, such as superficial rust or cosmetic damage, that do not affect safety. These racks are safe for continued use but may require routine monitoring.
Amber (Monitor): Signals moderate issues, like a slightly bent beam or loose bracing, that require repair within a specified timeframe (e.g., four weeks) to prevent escalation to a higher risk level.
Red (Urgent Action): Denotes critical issues, such as a cracked upright or severely damaged frame, posing an immediate safety hazard. These racks must be offloaded and repaired or replaced promptly.
Common Racking Issues
Overloaded racks beyond capacity: Exceeding weight limits can weaken racking structures, leading to potential collapses. Regular checks ensure loads align with manufacturer specifications.
Damaged uprights or beams: Impacts from forklifts or heavy loads can cause dents or bends, compromising stability. Early detection prevents costly repairs or accidents.
Improper bracing or anchoring: Missing or loose braces and anchors reduce racking stability, increasing the risk of tipping. We verify all components are correctly installed.
Tip: Train staff and have a designated PRRS to spot early signs of damage, such as visible dents or unusual noises during loading.
What Our Customers Have To Say
Contact Us to Schedule Your Inspection
We serve clients across the UK. Costs vary by warehouse size—get a tailored quote today!
Frequently Asked Questions
How often should racking be inspected?
Typically annually, or more frequently based on usage.
What if a Red risk is found?
Immediate action is required to repair or replace the racking.
Are inspections legally required?
They help ensure compliance with HSE regulations like HSG76.